History
We would like to introduce the history of our company's TBM business.
(Current Kanadevia Corporation)
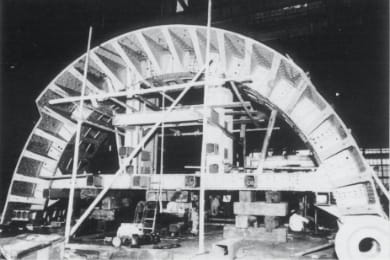
It is the first machine that inspired Kawasaki Heavy Industries to develop and manufacture a TBM. The roof TBM was adopted for the first time in Japan for subway tunnel construction. It was used for excavation of about 231m from Kokkai-Gijidomae Station toward Shinjuku on Marunouichi Line.
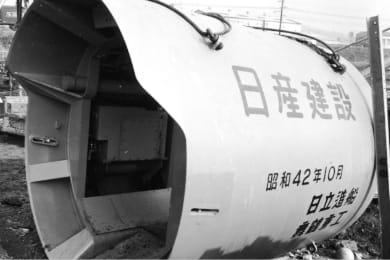
Hitachi Zosen Corporation developed and manufactured an Open hand drilling type TBM by using the technology cultivated in the shipbuilding industry. The TBM was used for sewerage construction project in Yokohama. Hitachi Zosen Corporation has solidified its position as a TBM manufacturer by receiving orders for more than 100 TBMs in about seven years from this year.
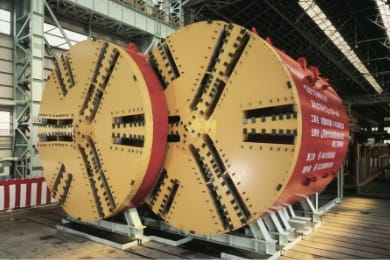
We delivered the world's first multi-face TBM, equipped with two circular cutter heads and an independent pressure chamber, for the Keiyo Line Kyobashi tunnel of JR East. Construction costs were reduced by excavating double-track tunnels at the same time. The completion of the machine required advanced design and manufacturing technology. It was the forerunner of the irregular shaped TBM.
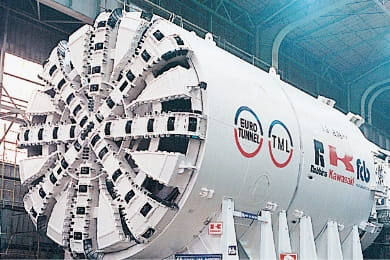
A soft ground / rock type TBM was introduced for excavation of the Dover Channel Tunnel. The 16km tunnel was excavated 8 months earlier than planned, and an additional 4km of excavation was requested, making a great contribution. 200 years after Napoleon's idea started, the TBM was the driving force behind the project that failed 26 times in the past.
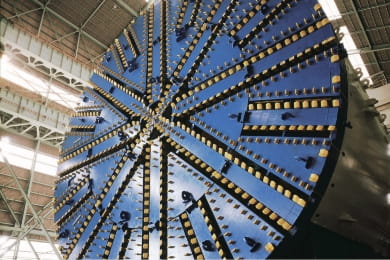
We delivered the world's largest slurry TBM at that time for the Tokyo Bay Aqua Line Highway. It was equipped with a fully automatic segment assembly device that we developed. The TBM performed high-speed excavation and recorded the longest excavation distance among the eight machines put into this project.
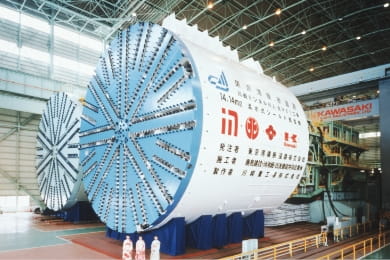
The TBM had the world's largest diameter at the time when it was put into the excavation of the undersea tunnel of Tokyo Bay Aqua Line Highway.
A total of 8 TBMs were used to excavate two 10km undersea tunnels, three of which were delivered by Kawasaki Heavy Industries. It was called "slurry type" because it mixes the excavated soil and water to make and discharge slurry.
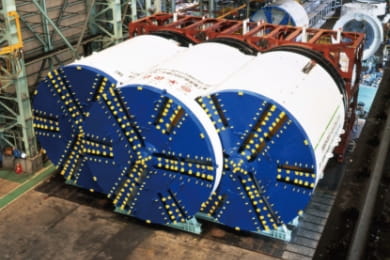
We developed the world's first triple circular cutter head TBM for construction at Osaka Business Park Station. The TBM excavated the platform and double track section simultaneously to build a station directly under the building. It was equipped with a special erector device. The main pillars that support the station after completion were also assembled in the TBM at the same time as the tunnel wall was constructed.
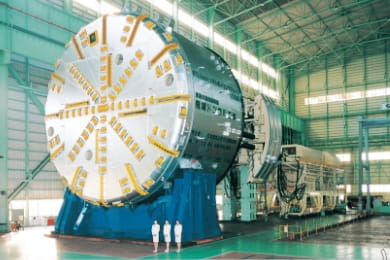
It was put into construction of the Hida tunnel on the Tokai Hokuriku Expressway. TBM is a machine that excavates the hardrock ground with a roller cutter attached to the cutter head. We have made improvements that can be applied not only to hardrock ground but also to a wide range of ground conditions including crush zones.
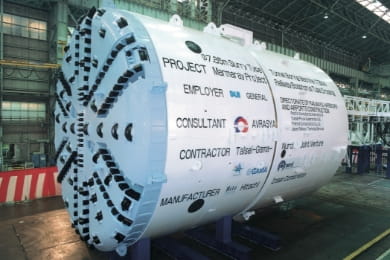
We delivered four TBMs for the railroad project crossing the Bosphorus Strait that connects the Asian and European continents, which has been a dream of the Turkish people for many years. In addition to rock excavation, the excavation was carried out under severe conditions with a maximum water pressure of 0.85 MPa.
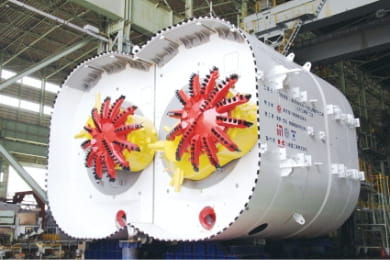
It was put into underground construction between Shibuya Station and Daikanyama Station on the Tokyu Toyoko Line. A non-circular TBM was required to secure the isolation distance between the sewage pipe and the tunnel as long as possible, and it was jointly developed with Kajima Corporation. It is a double cutter head machine with double blades, with the revolving cutter head and revolving drum. "Aporo cutter" means "All potential Rotary Cutter".
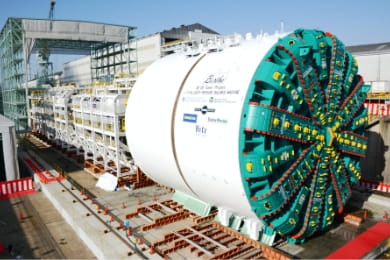
The TBM named "Bertha" was delivered for the road tunnel project in Seattle, USA. The TBM completed the excavation of road tunnel in 2017. We delivered full back-up equipment for the world's largest TBM project.
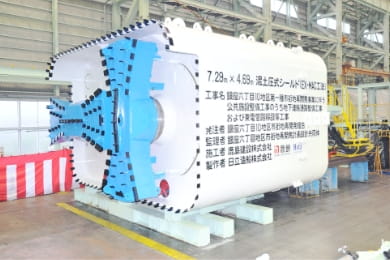
A TBM was delivered for a passage tunnel project from Ginza Station to GINZA SIX. In order to make effective use of the narrow underground space in Ginza, the rectangular TBM was required. It excavated under the depth of only 2.6m below the ground of the big city without affecting the surface. You can see the machine-assembled segments through the completed underground passage tunnel.
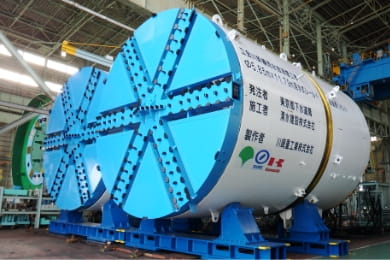
The H&V TBM was used for Tachiai River Drainage Channel project. Spiral construction is a construction method that the TBMs, which initially excavated in two horizontal rows, twist and change its posture to two vertical rows, or changes from two vertical rows to two horizontal rows as it excavates. Two TBMs with a diameter of 5.85m performed spiral construction while maintaining a distance of only 9cm to each other, and excavated along with the river line.
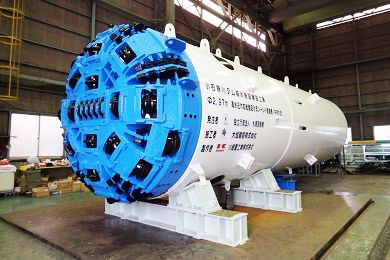
The TBM was used for the construction of a drainage tunnel connecting the Sada River and the Koishiwara River in the Chikugo River area of Fukuoka Prefecture. In addition to the hard rock, we challenged the difficult condition of design water pressure 2.0Mpa with two TBMs that had been manufacturered with our technology accumulated over many years, and excavated a total of 5km.
2021
Kawasaki Heavy Industries Ltd. and Hitachi Zosen Corporation integrated the TBM business and newly established "Underground Infrastructure Technologies Corporation"